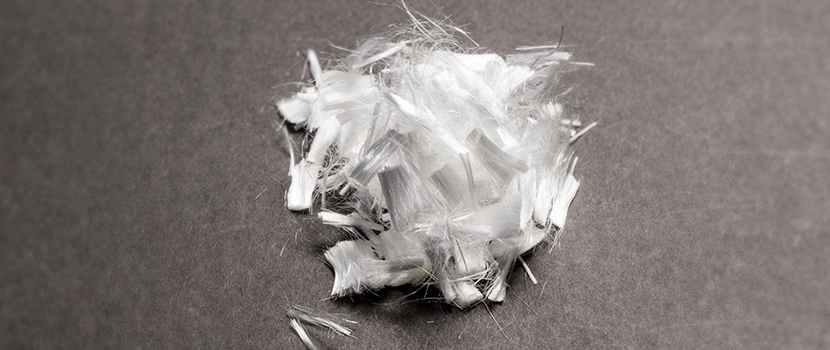
Our strengths
1. More than 30 years’ experience
Having been in the business of polypropylene fibre production since the mid 1980s, you can trust that we have the required expertise and knowhow to find the optimal fibre solution to your need.
1. More than 30 years’ experience
Having been in the business of polypropylene fibre production since the mid 1980s, you can trust that we have the required expertise and knowhow to find the optimal fibre solution to your need.
Save on costs and time – and get a better end result – with the unique quality features of Danish® Fibres. To share some key examples:
• < 1% air intake in concrete
For the production of construction fibres, we use a special mix, which reduces the air content in concrete to about 1% – much less than competitive polypropylene fibre products can offer.
• Prevention of static electricity
When producing fibres for filters, we manufacture at a slow speed to avoid the occurrence of static electricity, which saves the customer from having to employ a special oil to remove the static electricity.
• Clean cuts
As a standard, we frequently change the blades in production to ensure clean cuts, which hinder fibres from sticking together.
Save on costs and time – and get a better end result – with the unique quality features of Danish® Fibres. To share some key examples:
• < 1% air intake in concrete
For the production of construction fibres, we use a special mix, which reduces the air content in concrete to about 1% – much less than competitive polypropylene fibre products can offer.
• Prevention of static electricity
When producing fibres for filters, we manufacture at a slow speed to avoid the occurrence of static electricity, which saves the customer from having to employ a special oil to remove the static electricity.
• Clean cuts
As a standard, we frequently change the blades in production to ensure clean cuts, which hinder fibres from sticking together.
We have optimised our production flow, to be able to respond quickly to customer requests and adapt our production to individual needs. We know that time is money for our customers, so delivery speed and meeting agreements are always our highest priority.
Also, we have a strong network of partnering suppliers, enabling us to easily scale our production to meet changes in demand.
We have optimised our production flow, to be able to respond quickly to customer requests and adapt our production to individual needs. We know that time is money for our customers, so delivery speed and meeting agreements are always our highest priority.
Also, we have a strong network of partnering suppliers, enabling us to easily scale our production to meet changes in demand.
We like to move forward and discover new fibre solutions in partnership with our customers. In 1985, we obtained the first ever patent in the world for polypropylene fibres aimed at crack control. Since then, we have not stopped innovating.
Examples of recent innovations are the on-site fibre cutter for construction sites, and the unique Wiking® Manilla fibre for stabilisation of soil in riding arenas.
We like to move forward and discover new fibre solutions in partnership with our customers. In 1985, we obtained the first ever patent in the world for polypropylene fibres aimed at crack control. Since then, we have not stopped innovating.
Examples of recent innovations are the on-site fibre cutter for construction sites, and the unique Wiking® Manilla fibre for stabilisation of soil in riding arenas.
To secure our customers the highest quality, we have developed a quality management system and continually seek to raise our standards further. As a result, we have gained a number of certifications, including the Allgemeine bauaufsichtliche Zulassung (abZ) – which is currently only held by three fibre production companies in the world.
To secure our customers the highest quality, we have developed a quality management system and continually seek to raise our standards further. As a result, we have gained a number of certifications, including the Allgemeine bauaufsichtliche Zulassung (abZ) – which is currently only held by three fibre production companies in the world.
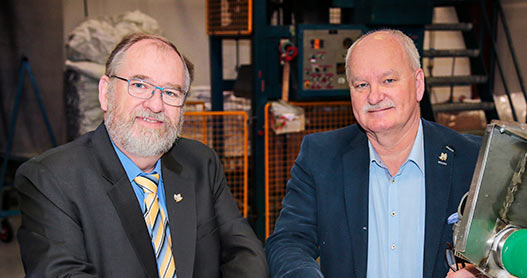